Powder Coated Aluminium Doors: Colours & Selection Guide
Table of Contents
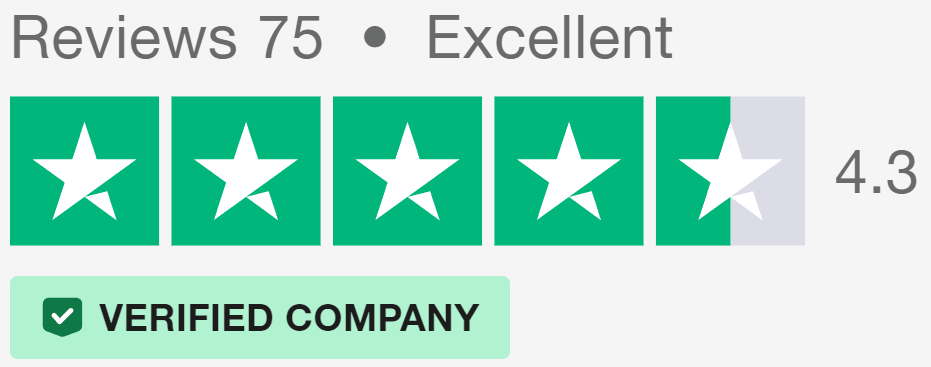
How Powder Coating Works on Aluminium Doors
Powder coated aluminium doors rely on a unique manufacturing method where dry powder paint particles bond directly with the metal surface. The raw aluminium surface undergoes thorough cleaning before specialists apply a charged powder that sticks to the frame through electrostatic attraction.
The Science of Powder Coating Aluminium
Raw aluminium needs careful preparation before coating begins. Specialists strip away surface oils and contaminants using phosphoric acid, which also roughens the metal microscopically to help the powder grip better. The powder itself contains pigments, resins, and other materials that melt together when heated, forming a tough shell around the frame.
Modern powder coating uses thermosetting polymers that permanently change their chemical structure during baking. These polymers cross-link as they cure, creating an incredibly hard finish that won’t melt again even under intense heat. The powder coating process happens in specialised spray booths where technicians control temperature and humidity precisely to ensure perfect adhesion.
The electrical charge between the powder and aluminium creates a molecular-level grip. When heated, the powder particles actually flow into the microscopic valleys created during preparation, physically anchoring themselves to the frame. This means powder coated aluminium doors resist chips and scratches far better than traditional paint finishes.
Protection Features
British weather demands robust door finishes, which makes powder coating particularly suitable. Salt spray from coastal areas won’t penetrate a properly applied coating, while UV rays bounce harmlessly off the surface instead of breaking down the finish. Looking at any colour chart for powder coated aluminium glass doors reveals hundreds of options, each offering the same high level of protection.
Factory Application Steps
The range of colours available stems from precise mixing ratios in modern coating facilities. Computerised systems measure each powder component exactly, ensuring batch consistency across large door orders. The coating booth’s automated guns spray evenly while the frame moves through on a conveyor, guaranteeing uniform coverage from every angle.
Powder Coated Aluminium Doors vs Other Finishes
Modern powder coated aluminium doors last decades longer than traditional paint finishes. The robust coating prevents metal oxidation, while painted surfaces often start peeling within a few years of installation.
Protection Against UV and Weather
Unlike anodised finishes that can fade unevenly, powder coating maintains its original colour even after years of sun exposure. The uniform thickness of powder coating, typically around 60 microns, creates a barrier that stops UV rays from reaching the metal beneath. Powder coated aluminium glass doors installed in coastal areas show particular resistance to salt spray damage, which often corrodes untreated or painted frames.
Extreme temperature changes pose minimal threat to powder coated surfaces. While standard paint might crack and peel during winter freezes, powder coating expands and contracts with the aluminium frame without losing adhesion. The coating’s flexibility comes from its molecular structure, which forms strong cross-links during the baking process.
Weather Performance Testing
Laboratory tests expose powder coated samples to accelerated weathering cycles that mimic decades of real-world conditions. Salt spray chambers replicate coastal environments, while UV exposure units simulate prolonged sunlight. These tests prove especially relevant for aluminium framed sliding doors, where smooth operation depends on coating durability.
Comparing Coating Types
Standard wet paint requires multiple coats and lengthy drying times between applications. In contrast, powder coating needs just one application, reducing production time and improving consistency. The single-coat process also eliminates runs, drips, and other common paint defects.
Paint regularly chips away from door frames, particularly around high-contact areas like handles and locks. The molecular bonding in powder coating creates a surface that resists impact damage. When properly applied, powder coated aluminium doors maintain their protective qualities even after years of daily use.
Texture Options for Frames
Anodising produces a metallic sheen that some homeowners find too industrial for residential settings. Powder coating offers subtle variations in texture, from ultra-smooth gloss to fine-textured matte finishes. The coating’s thickness determines the final texture – thinner layers create smoother surfaces, while building up multiple passes produces deeper textures.
Matte finishes hide minor scratches better than glossy surfaces, making them practical for busy households. The textured surface disperses light rather than reflecting it directly, helping to mask small imperfections that might develop over time. Satin finishes strike a balance between durability and sophistication, with a subtle sheen that complements modern architecture.
Surface Quality Assessment
Close inspection of powder coated surfaces reveals their superior uniformity compared to wet paint. The electrostatic application process ensures complete coverage, even in hard-to-reach corners and edges. Manufacturing defects like orange peel texture – common in liquid paint – rarely occur with powder coating when applied correctly.
Professional installers check coating thickness with electronic gauges to verify proper coverage. These measurements ensure the protective layer meets industry standards for durability. Regular quality control during production keeps powder coated aluminium doors consistent across large manufacturing batches.
Regular exposure to cleaning products can degrade traditional paint finishes over time. The chemical resistance of powder coating means homeowners can clean their doors without worrying about damaging the surface. Even strong detergents used to remove stubborn stains won’t compromise the coating’s integrity.
Colours for Powder Coated Aluminium Doors
Modern powder coated aluminium doors come in virtually any colour imaginable, though certain shades remain consistently popular in British homes. Dark tones like anthracite grey dominate current installations, particularly in urban areas where contemporary architecture prevails.
Popular RAL Colours
Neutral colours remain the safest choice for lasting style. RAL 7016, a deep charcoal shade, appears in increasing numbers of new installations. White powder coated aluminium glass doors (RAL 9016) are common too, chosen primarily for period properties where traditional aesthetics matter most.
Recent years have seen growing interest in metallic finishes. Pearl bronze and champagne colours add subtle depth compared to standard flat shades. These metallic options catch light differently throughout the day, creating visual interest without appearing ostentatious.
Brown patio doors continue their steady popularity, especially in rural settings. Earth tones like RAL 8017 (chocolate brown) match natural stone and timber elements while providing superior weather resistance. The rich depth of powder-coated browns surpasses that of painted or stained wooden frames.
Dark Frame Colour Effects
Black framed doors make a bold architectural statement, though careful planning prevents them from overpowering smaller spaces. The crisp lines of powder coated aluminium doors in jet black (RAL 9005) work particularly well against light-coloured walls, creating striking visual contrast.
Dark colours absorb more heat from sunlight, potentially causing thermal expansion in frames. However, modern powder coating formulations include heat-reflective pigments that reduce this effect. These specialised coatings keep surface temperatures manageable even in direct summer sun.
Light Transmission Factors
Darker frames can reduce the apparent size of glass panels, while lighter colours seem to disappear into their surroundings. This optical effect proves especially important when choosing finishes for coloured bifold doors, where multiple frames sit adjacent to each other.
Light Frame Design Choices
White and cream powder coated frames suit traditional properties perfectly, maintaining period character while offering modern performance. These lighter shades reflect more natural light into interior spaces, brightening rooms naturally without artificial lighting.
Pale greys provide an excellent middle ground between stark white and darker finishes. These subtle tones complement most architectural styles while hiding dust and fingerprints better than pure white. RAL 7035 and 7040 rank among the most requested light grey options.
Special Finish Options
Textured powder coatings add another dimension to colour selection. Fine-textured finishes resist minor scratches better than smooth surfaces, making them practical for high-traffic areas. These specialised coatings maintain their appearance longer than standard smooth finishes.
Dual-colour options allow different shades inside and out. Many homeowners choose darker external colours for contemporary kerb appeal while selecting lighter internal finishes to brighten living spaces. This approach combines style flexibility with practical benefits.
Metallic and pearl finishes require specific application techniques to ensure consistent appearance. The metallic particles in these powder coatings must align uniformly during application. Proper application technique prevents streaking or mottling in the final finish.
The powder coating process allows precise colour matching between different door components. Handles, hinges, and other hardware items receive identical treatment to main frame sections. This uniform approach creates cohesive overall appearance impossible with other finishing methods.
Common Powder Coating Problems
Manufacturing quality varies widely among powder coated aluminium doors, with some manufacturers cutting corners in the preparation and application processes. Poor surface preparation leads to premature coating failure, while rushed curing can cause immediate adhesion issues.
Spotting Poor Quality Coating
Uneven colour distribution often indicates improper application technique. Professional powder coated aluminium glass doors should display consistent colour across all surfaces, without lighter or darker patches. Running your hand along the frame reveals texture inconsistencies – properly coated surfaces feel smooth and uniform throughout.
Bubbling or orange peel textures in the finish point to incorrect curing temperatures. When ovens run too hot, the powder coating boils instead of flowing smoothly. These surface defects create weak points where moisture can penetrate the protective layer.
Visual inspection under bright light exposes common application flaws. Powder coated aluminium doors should not show spray patterns or tide marks. These telltale signs suggest rushed application or poor operator technique during the coating process.
Testing Coating Durability
Professional installers use calibrated tools to measure coating thickness. Readings below industry standards indicate insufficient coverage, while excessive thickness can cause cracking. Proper thickness ensures optimal protection without compromising the door’s operation.
Microscopic examination reveals the quality of surface preparation. Inadequately cleaned aluminium prevents proper powder adhesion. Salt spray testing demonstrates how well powder coated aluminium bifold doors resist corrosion – quality coatings withstand hundreds of hours without deterioration.
Colour Matching Between Panels
Large installations require careful batch control to maintain colour consistency. Different production runs can show subtle variations, particularly in metallic finishes. Professional manufacturers keep detailed records of powder formulations and application parameters to ensure repeatability.
Powder coating chemistry changes slightly during extended storage. Manufacturers must regularly test and adjust their processes to compensate for these changes. Failure to maintain strict quality control results in visible differences between door panels produced at different times.
Environmental Damage Signs
Coastal locations pose unique challenges for powder coated surfaces. Salt-laden air accelerates corrosion where coating coverage falls below specification. Regular cleaning prevents salt accumulation in frame corners and joints.
UV exposure gradually breaks down the polymer structure in powder coatings. Premium grade powders contain UV stabilisers that extend service life, while budget formulations may show early signs of degradation. South-facing installations need particularly high-quality coatings to maintain their appearance.
Chemical exposure from building materials can degrade coating integrity. Fresh concrete and mortar contain highly alkaline compounds that attack powder coatings. Protection during construction prevents permanent damage to door frames.
Choosing Your Powder Coated Aluminium Doors
Selecting colours for powder coated aluminium doors requires careful thought about your home’s overall design scheme. Green might seem an unusual choice, but sage and olive tones work beautifully with natural stone facades and garden settings.
Matching House Styles
Georgian and Victorian properties often benefit from subtle cream or off-white finishes that complement original architectural features. Modern powder coated aluminium glass doors in heritage colours maintain period authenticity while providing superior durability to painted timber alternatives.
Contemporary homes give greater scope for bold colour choices. Powder coated aluminium sliding doors in stark contrasts – like black frames against white walls – create strong architectural statements. Slim frames in darker shades appear to float within large glass panels, drawing attention to views rather than the frame itself.
The surrounding landscape should guide colour selection. Urban settings often suit industrial-inspired finishes like gunmetal or bronze, while rural locations might call for softer earth tones. Properties near water can mirror the environment with blue-grey powder coatings that echo sky and sea.
Architectural Elements
Window colours must coordinate with door finishes for visual harmony. Black sliding doors need matching window frames to maintain design consistency. This approach creates a unified look across all glazed elements of the building.
Roof tiles and brickwork provide natural colour cues. Red-toned bricks work well with warm grey or bronze powder coatings, while slate roofs pair naturally with darker frame colours. These relationships help anchor large glass installations within the building’s overall composition.
Testing Colours On-Site
Natural light changes throughout the day, altering how powder coated surfaces appear. Morning sun brings out warm undertones, while evening light might emphasise cooler aspects of the same colour. Sample panels viewed at different times reveal these subtle variations.
Artificial lighting poses additional challenges for colour selection. Halogen, LED, and fluorescent sources each render colours differently. Testing under actual installed lighting prevents surprises after installation. Large powder coated aluminium doors look remarkably different under various light sources.
Surrounding materials influence colour perception. Glass reflections can lighten the apparent shade of door frames, while shadows from overhanging structures might darken them. Professional installers often bring sample panels to compare against existing building materials.
Custom Finish Possibilities
Standard RAL colours provide hundreds of options, but custom finishes offer unlimited possibilities. Mixed-to-order powder coatings match corporate branding or specific design requirements. These bespoke options typically cost more and require longer lead times than standard colours.
Manufacturing custom colours demands precise control over pigment ratios and processing conditions. Small variations in temperature or humidity can alter the final appearance. Reputable manufacturers maintain detailed records of custom formulations for future matching needs.
Specialist finishes like metallic or pearl effects need careful handling during application. The metallic particles must align consistently to avoid streaking or mottling. These premium finishes often require specific application techniques and experienced operators.
Colour Psychology in Design
Room size perception changes with frame colour choice. Dark powder coated frames can make spaces feel more intimate, while lighter shades create an airier atmosphere. This principle proves especially important when selecting finishes for smaller rooms.
Neutral tones provide long-term flexibility as interior colour schemes change. Greys and browns coordinate easily with evolving design trends, while bold colours might limit future decorating options. Investment properties often benefit from this approach.
Colour temperature influences room ambience. Cool greys suit minimalist interiors, while warmer bronze or copper tones create more inviting spaces. These subtle differences become more pronounced in larger installations where frames form significant visual elements.
Professional colour consultants often recommend viewing large installations of similar products. Seeing powder coated aluminium doors in completed projects provides valuable insight into how different finishes work in real-world settings. This approach helps prevent costly colour selection mistakes.
We’d Love to Help You
Vision Glass Doors is a designer, manufacturer, and installer of premium door systems. We are a family run business with over 20 years’ experience and 5,000 installations across the UK.
Our leading range of door systems include Ultra Slim – Slide and Turn Doors, Slimline Sliding Patio Doors and Frameless Glass Doors. Suitable for various internal and external applications, they are applicable to residential and commercial projects.
Click Quick Quote Online for a free quotation within 24 hours. Alternatively, call or email us on 01582 492730 or at info@visionglassdoors.co.uk.
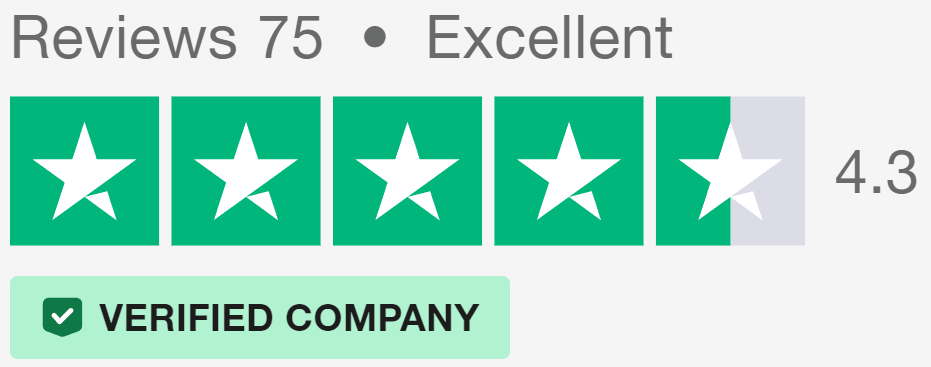